国内比率増える
工場の生産を仕切っている石井辰佳グローバルモノづくり総括部長は「為替の影響などもあり、国内の生産比率が増えてきている」と話す。同社では季節変動が大きいスマホ向けや、電装関連など季節変動の少ない分野などにも幅広く実装機を生産することで工場全体の安定的な稼働に結びつけている。
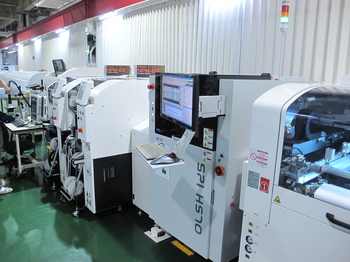
この工場ラインでは約1000人が働いている。驚くべきはその大半は旋盤やフライス盤などモノづくりの基礎となる国家資格を取得していることで、それも1つではなく2つ以上複数取得している。さらに工程管理の技術を習得した会社の認定資格としてIE(インダストリアル・エンジニアリング)認定を行っている。つまり、ITとモノづくりの両方が分かった技術者がラインで働いている。従業員は自分の技術に満足することなく日々研鑽に努めているようで、これが日進月歩のITの世界にあって技術力の維持向上につながっている。それでも石井統括部長は「いかに短期間に良品を納入できるかが重要で、これまでの実績があるからといって油断はできない。顧客に対してどれだけトータルサポートできるかが決め手になる」と指摘する。
3つの「つながり」
日本の製造業の生産ラインでは熟練技術者が若手社員を指導する形で製造ラインの効率を上げてきたが、熟練技術者も高齢化を迎えて、技術の伝承も難しくなっている。いままでは困難といわれてきた匠の技術も計測技術の応用により数値化できるようになり、新しい実装ラインの現場ではこうした動きも組み込まれてきている。結果として、ラインは極力人手をかけないようにしてフロアごとに一括して管理する「統合フロアマネジメント」方式に変わろうとしている。
ITをモノづくりの現場に生かした典型的な例が新幹線の先頭車両形状だ。JR東海によると、加工が難しいといわれていた「N700系」車両の流線型の先頭部分は、熟練工がハンマーをたたいて作っていた。だが13年2月にデビューした最新型の「N700A」になってからは、熟練工の手を借りなくてもすべてITを応用した機械で削りだすことができるようになったという。
中でもパソコン、スマホなど携帯電話、自動車関連部品など電子部品を組み合わせて作る製造ラインでは、この方式の導入が進みつつある。リポートしたパナソニックの場合が典型で、PFSCの電子部品実装ディビジョンの島田篤人IFM事業開発部長は「設備と設備、工場内の各エリア、取引先・エンドユーザーの3つの『つながり』を持たせることで迅速な意思決定と、それを実現するモノづくり体制ができる」と強調する。
「統合フロアマネジメント」では、実装の後工程や検査・組み立てなどすべての作業データとして蓄積されており、このデータを蓄積分析してどこ工程でどのような状況でエラーが出たかを瞬時につかむことができる。その上で、工場と工場が生産に関するデータをリアルタイムで情報共有し、良品を最少人数で安定的に効率よく生産できる。これを取引先やグローバル展開しているほかの工場とつなぐことで、グローバルレベルでの最適生産が可能になる。その先には、いまは人間が手作業で行っているような仕事がロボットに置き換わる可能性があるかもしれない。